Parametric optimization of aircraft landing gear lugs
Landing gear lugs are one of the important components in an aircraft as they provide connectivity between two different components. Many lugs are present on a landing gear and on the aircraft as a whole. These lugs are subjected to many severe loading conditions during its operating life cycle. Most of the times, a safety factor is applied to the conditions that are difficult to simulate and the lugs end up being over designed, affecting the weight of the aircraft. Objective of the project was to optimize the geometry of the lug to get required static and fatigue strength with minimum possible weight.
Software Used: MATLAB and ABAQUS

PROBLEM FORMULATION:
A lug is to be designed with following features:
-
Light weight
-
Sustain static loads exerted during aircraft landings and take-off
-
Sustain Temperature Fluctuations
-
Sustain Fatigue Loads

Inter-relationship between various design criteria is depicted in the following flowchart:


COMPUTATIONAL MODEL AND VALIDATION:
Based on the above inter-relations, a computational model to design the lug was developed in MATLAB. The model considered static analysis of lugs by Air force method, fatigue analysis, thermal analysis and material properties based on loading direction. The model was validated using high fidelity ABAQUS FEA.
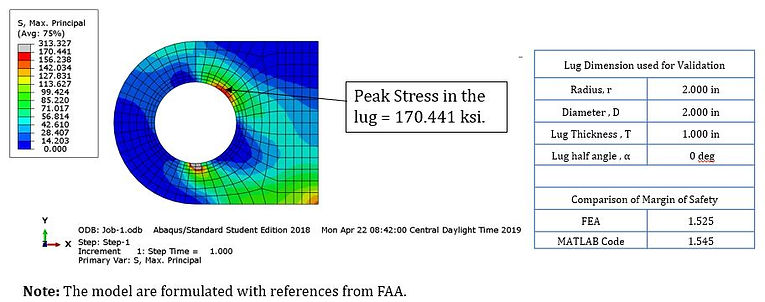
SINGLE OBJECTIVE OPTIMIZATION:
The lug design was optimized for its weight, with constraints on other design criteria. Optimization problem is summarized in the chart below:

Results of gradient based and genetic optimization algorithms are depicted in the graphs below:


Both algorithms converged at same point:
X = (r, D, t, α) = (1.2423 in, 0.8282 in, 0.8282 in, 0.000 deg)
J = (W) = 1.4646 lbs
MULTI OBJECTIVE OPTIMIZATION:
To identify a compromise between weight and the strength, multi objective pareto analysis was performed. The graph indicates various possible designs and the utopia point (Most desirable scenario).
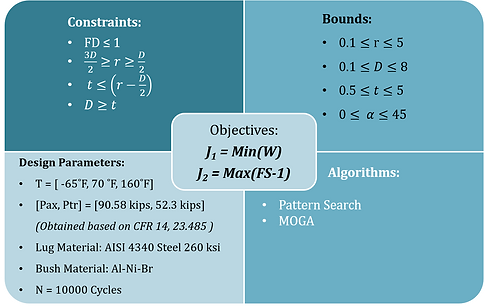
